What is a Blow Moulding Machine?
Blow moulding machines are used to manufacture a wide range of plastic products, including bottles, containers, and other hollow shapes. There are several different types of blow molding machines, including extrusion blow molding, injection blow molding, and stretch blow molding.
Blow molding, also known as hollow blow molding, is a rapidly developing plastic processing method. A tubular plastic parison made of thermoplastic resin is molded by extrusion or injection. While still hot or softened by heat, it is placed in an open mold and immediately inflated with compressed air inside the parison, causing the plastic to expand and tightly adhere to the inner walls of the mold. After cooling and demolding, various hollow products are obtained. The manufacturing process of blow-molded films is similar in principle to that of hollow products, but molds are not used. Here, we recommend our Hollow Blow Molding Machine.
We have a good understanding of customer needs and provide professional blow molding machine solutions. We would like to be your reliable support partner. If you need to buy a blow molding machine, welcome to contact us!
Can blow molded plastic be recycled?
Yes, blow molded plastic can be recycled. Blow molding is a common manufacturing process used to create plastic products such as bottles, containers, and automotive parts. These products are typically made from polyethylene (PE), polypropylene (PP), or polyethylene terephthalate (PET) plastics, which are all recyclable materials.
The recycling process for blow molded plastic involves shredding the plastic into small pieces, melting it down, and reforming it into new products. However, it’s worth noting that not all recycling programs accept all types of plastic, so it’s important to check with your local recycling program to see if they accept blow molded plastic and if there are any special instructions for preparing it for recycling.
Additionally, it’s important to ensure that the plastic is properly cleaned and free from any contaminants before recycling. This helps to ensure that the recycled plastic is of good quality and can be used to create new products.
Blow Molding vs Injection Molding: What’s the Difference?
The terms “blow molding” and “injection molding” are often interchangeable when referring to molding processes. While similar, though, they aren’t necessarily the same. Both blow molding and injection molding involve the use of liquid material — typically plastic — that’s forced into a mold cavity. The difference is that blow molding is used to create hollow objects, whereas injection molding is used to create solid objects. For hollow objects, only blow molding offers a fast and effective solution for manufacturing companies.
Why Opt for the Blow Moulding Process?
The main benefit of using the blow moulding plastics process in manufacturing projects is the sheer number of products that can be made using any of the three flexible, efficient methods. Plastic food containers can remain hygienic and attractively branded, while shampoo bottles and soap dispensers offer excellent chemical resistance and the ability to form complex shapes. Automotive ducting and industrial tubs and drums provide robust, durable strength for use in heavy industry, construction and other demanding environments. The medical sector prizes the manufacturing method for its easy sanitization properties and lightweight. Put simply, plastic blow molded products are commonly found in multiple areas of domestic and commercial life.
Other advantages include the fact that extrusion blow moulding, in particular, can produce complex and highly bespoke shapes that can be accurately designed for precise sizes, finishes and wall thicknesses. For example, bottlenecks must match the grooves of the bottle top exactly to ensure a watertight seal once the cap is screwed on. Finished products tend to be of very high quality, yet tooling and manufacturing costs usually remain lower than other types of plastic manufacturing processes, which certainly helps the bottom line.
Disadvantages include the fact that there are limits to how much difference can be made in wall thicknesses due to the fact that the products must be hollowed out yet retain sufficient strength and integrity. Products can also be harder to recycle if thermosetting polymers are used. This is because such materials can only be reshaped once and will no longer be able to be softened or melted for reforming or recycling after that.
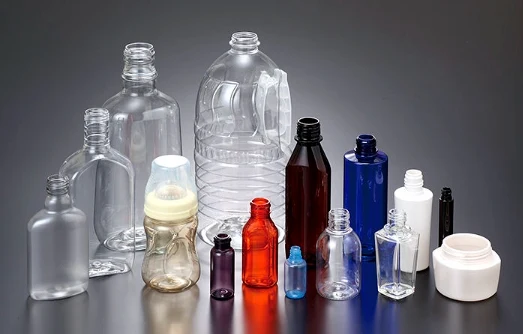
The Benefits of Using Blow Molding Machines
Despite the numerous advantages of the molding, there are also some challenges associated with this manufacturing process, including:
① Environmental concerns
One of the most pressing challenges associated with blow-molded plastics is environmental concerns. The production of plastics generates significant amounts of waste and pollution, and improper disposal of these materials can have serious consequences for the environment. Recycling is one solution to this problem, but not all types of plastics can be easily recycled, and the cost of recycling can be prohibitive for some manufacturers. Improving waste management practices and finding innovative ways to recycle and reuse plastic materials are critical steps in reducing the environmental impact of blow-molded plastics.
② Limited color options
Another challenge associated with blow-molded plastics is the limited color options available for these materials. The manufacturing process can make it difficult to achieve certain colors and shades, which can be a limitation for manufacturers who want to create products with specific aesthetic or branding requirements. Some manufacturers may turn to other materials or processes to achieve their desired color scheme, which can increase costs and complexity.
③ Complex shapes
Complex shapes are also a challenge for blow-molded plastics. While this process is well-suited for producing simple, symmetrical shapes, it can be more difficult to achieve complex, irregular shapes. This is because the process relies on the use of molds, and creating molds for complex shapes can be expensive and time-consuming.
④ High production costs
Finally, high production costs for small quantities can also be a challenge for manufacturers using blow-molded plastics. The specialized equipment and tooling required for this process can make it prohibitively expensive for small-scale production runs. This can limit the ability of small businesses to use blow-molded plastics in their products and can result in higher costs for consumers.
In conclusion, blow-molded plastics play a crucial role in many industries, and the benefits they offer will continue to drive demand for this material. By addressing the challenges associated with the manufacturing process and developing more sustainable practices, the industry can continue to grow and thrive while minimizing its environmental impact.
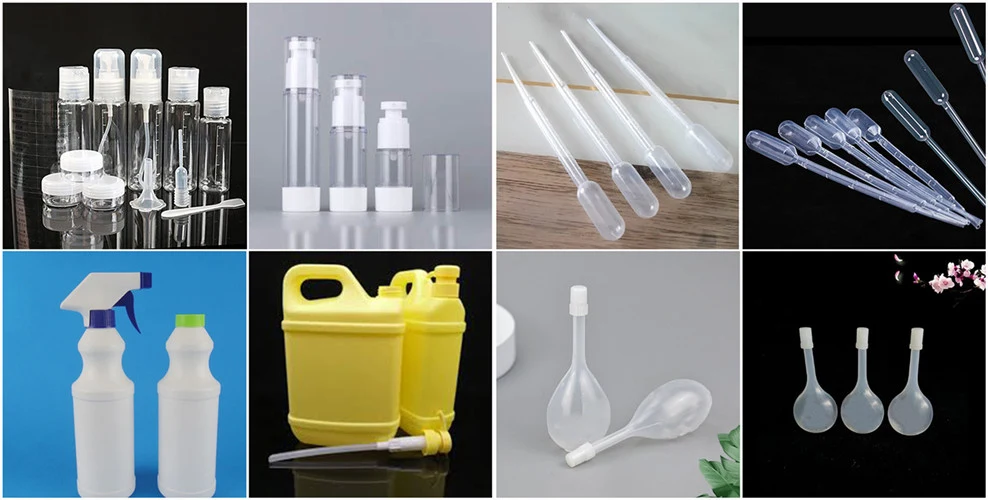
Common Problems And Solutions In The Blowing Process Of The Bottle Blowing Machine
1. What should I do with the bottom of the bottle blown by the bottle blowing machine?
The common factor for bottle accumulation is that the stretching rod is not adjusted in place. It is recommended that the stretching ratio between the preform and the bottle body is preferably 1:2.5 (excluding the mouth part), and at the same time adjust the heating temperature to extend the pre-blowing.
2. What should I do if the bottle’s mouth-blown by the bottle blowing machine is deformed?
Bottle mouth deformation Generally, during the heating process of the preform, the transmission chain drives the bottle base to transfer the temperature to the preform mouth. During the heating process, the temperature continues to accumulate, and the bottle mouth bulges and deforms. It only needs to increase the air-cooling or water-cooling of the bottle mouth. If the customer’s conditions permit, you can refer to the imported machine to install central air-conditioning in the production workshop to keep the ambient temperature of the workshop at an average temperature.
3. How to operate the bottle blowing machine, and which accessories should be checked?
As long as the equipment is controlled strictly following the method in the instruction manual and the performance of each safety door is checked regularly, the equipment as a whole is safe. However, the most significant hidden danger of the equipment is mainly on the seals of the water jacket and air jacket. For example, the water and air jackets are damaged, and the maintenance works are more troublesome.
4. How much chiller is needed for the carbonated beverage bottle blowing machine to blow the bottle?
The chiller for the carbonated bottle is about five times larger than the chiller for the water bottle. A simpler algorithm can be calculated at 1200 bottles/hp; for example, 36000 bottles/hour can equip with a 30-hp chiller. To ensure the stress requirements of the carbonate bottle bottom, the cooling time is generally 1.2 seconds, and the bottom mould temperature is 11 degrees. The number of lamp zones in the heating furnace can refer to the configuration of the hot filling machine, and the adequate heating time of the preform should be no less than 33 seconds.
5. What is the highest temperature resistance of the non-crystalline bottle mouth of the hot-filling bottle blowing machine? How many grams of preforms are needed?
At present, the preform mouths used in the production of hot-filled bottles in the industry are generally divided into crystalline mouths and non-crystalline mouths, and non-crystalline mouths are divided into 28 months and 38 months.
As far as the bottle mouth is concerned, the crystalline mouth can withstand 100 degrees without deformation, but the upper limit of heat resistance of the non-crystal mouth is only 92 degrees.
The preform and grammage used for blowing the medium-temperature bottle are best selected according to the requirements of hot filling. Suppose it is designed according to the single-mode 1700 bottles/hour. In that case, the single-mode cycle is 2.1 seconds, of which 1/4 of the time is the time to unlock the mould, and the remaining 3/4 of the time is the processing time, minus the balance; sealing, stretching, and pre-blowing is 0.2 seconds. The time for high-pressure forming and pressure-holding crystallization is only 1 second, the time for cold blowing and setting is 0.3 seconds, and the time for closing and closing is 0.1 seconds.
The time allocation mentioned here is only a reference value, and the specific time should be adjusted and guaranteed in real time through the control panel during production.
Strictly speaking, compressed air must be processed by a freeze dryer before it can be used for high blowing and cold blowing. Because the pipeline between the air compressor and the bottle blowing machine is long, to avoid the exposed pipeline from being exposed to the sun, The compressed air pipeline used for cold blowing and shaping must be cover with thermal insulation cotton to ensure that the temperature of the air source is not affected.
Summary: The above are the most common problems in the use of the bottle blowing machine. The bottle blowing machine causes different bottle problems during the blowing process. On the one hand, it is related to the structure of the bottle blowing machine itself, and on the other hand, it is the problem of debugging and use. , Most of the faults are caused by improper use of human factors. When you encounter problems, don’t worry; carefully analyze the problematic points of the blow moulding machine fault, carry out troubleshooting one by one or consult the sales service engineer of the blow moulding machine manufacturer.
Blow molding and injection molding are two popular methods for creating plastic parts. At YOULI,, we offer custom plastic injection molding solutions developed with quality and efficiency in mind. YOULI, a leading Pet Bottle Mold Maker and trusted supplier of Bottle Blowing Machines embraces a corporate culture rooted in integrity, innovation, and excellence. If you think injection molding might be a good solution for your next project, get in touch with our team or request a quote today.